Glowing About Glass Jaison Staines On Bending Neon
Neon was invented by Frenchman, Georges Claude in 1902 – he had a workshop where he trained people as neon makers and supplied handmade signs. He patented it and introduced it to the US, and by the 30s and 40s, it really took off. So for decades now, neon signs have lit up every corner of urban life – and their appeal does not dim.
Glyphics’ neon specialist, Jaison Staines decided to move to London from South Africa in 2008, and has been working here as a neon sign maker for more than ten years now. He grew up in a wonderland of neon, salvaged by his own hands and proudly displayed in the sanctuary of his boyhood bedroom. The son of a master glassblower (a time hardened, exceptionally skilled worker of the craft), it seems his destiny was preordained in bright, radiating lights.
Despite initially deciding to take his own path, he now finds himself transforming commissions into beautiful original artworks, bringing that little bit of night club heat or jazz bar cool to our client’s spaces…
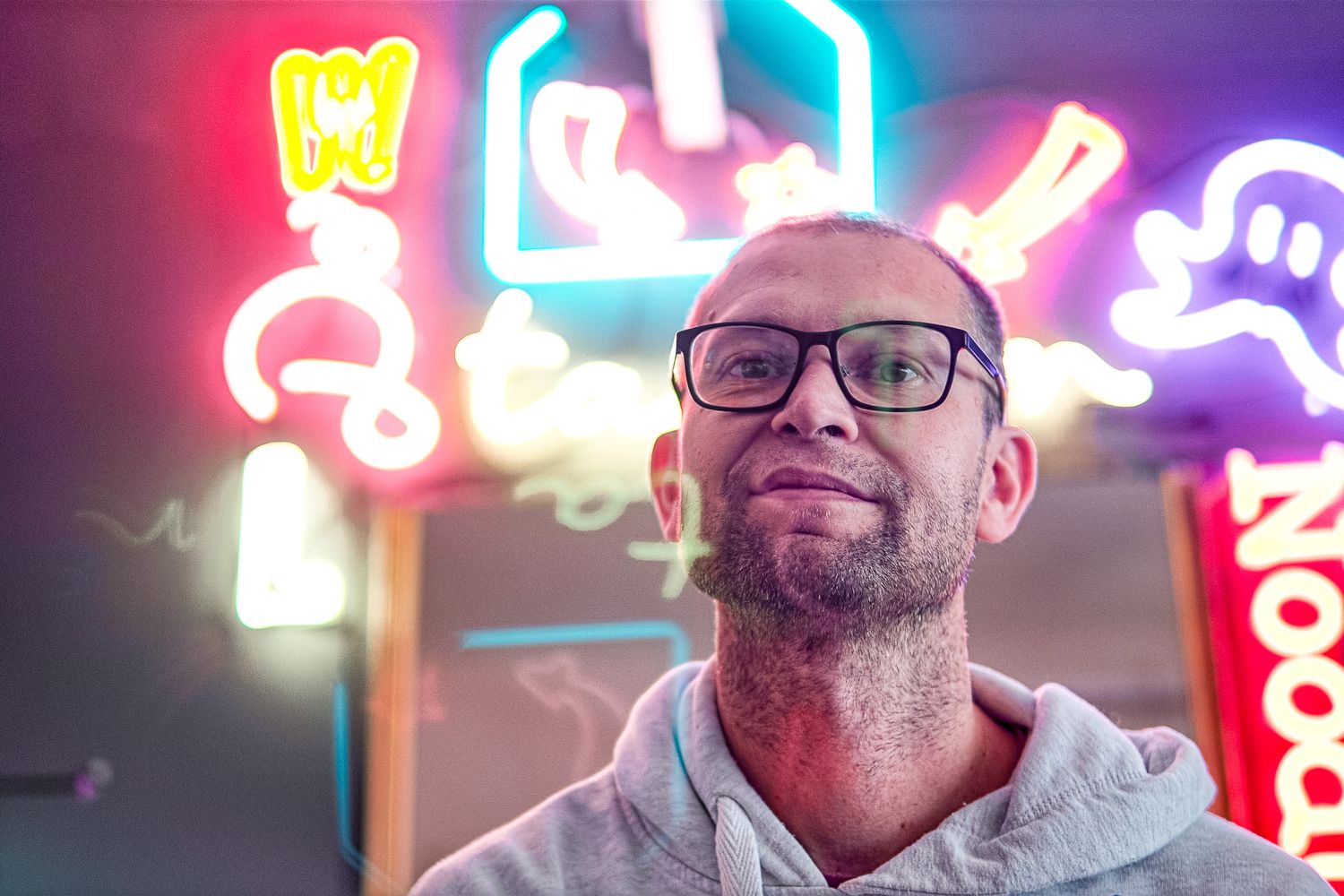
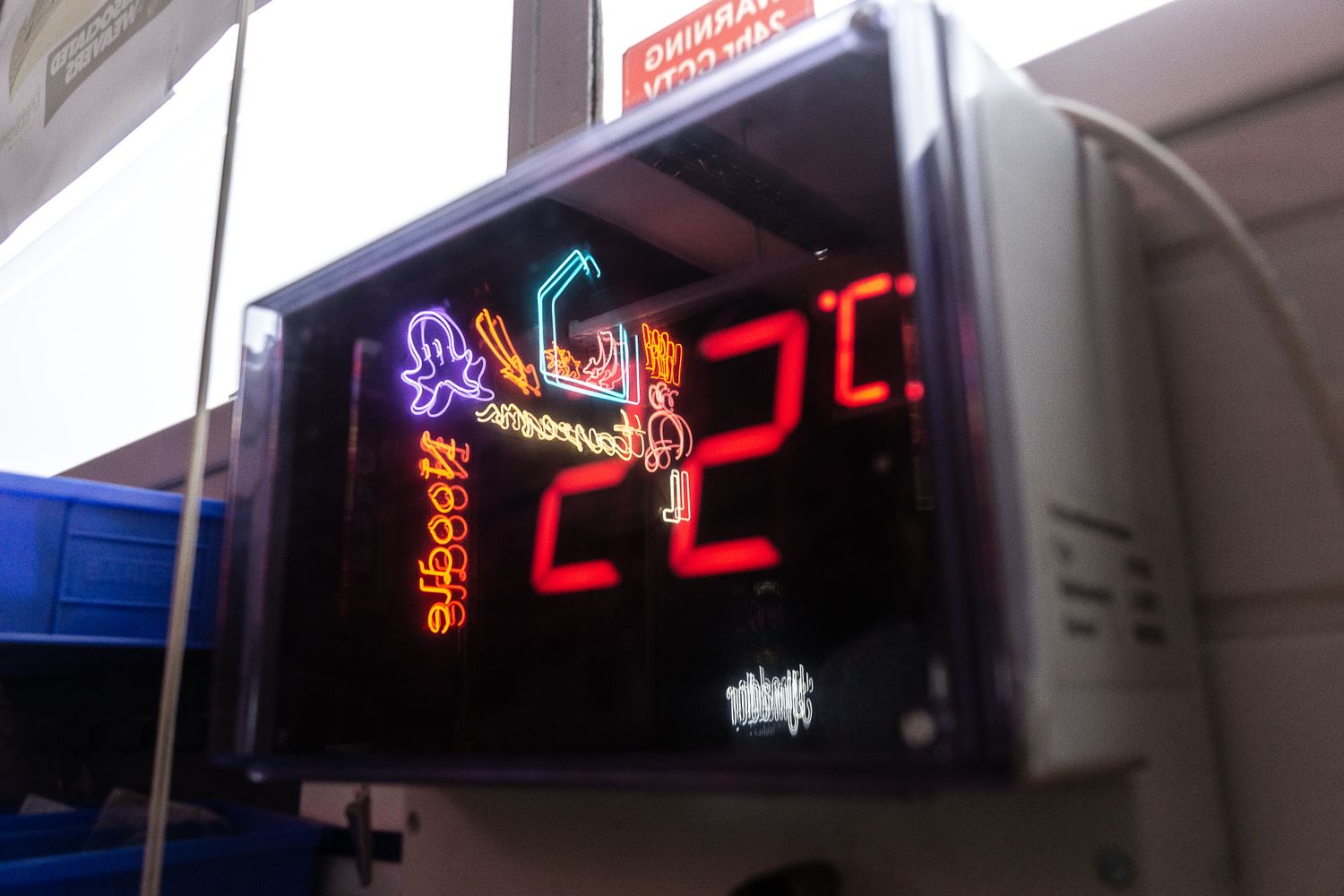
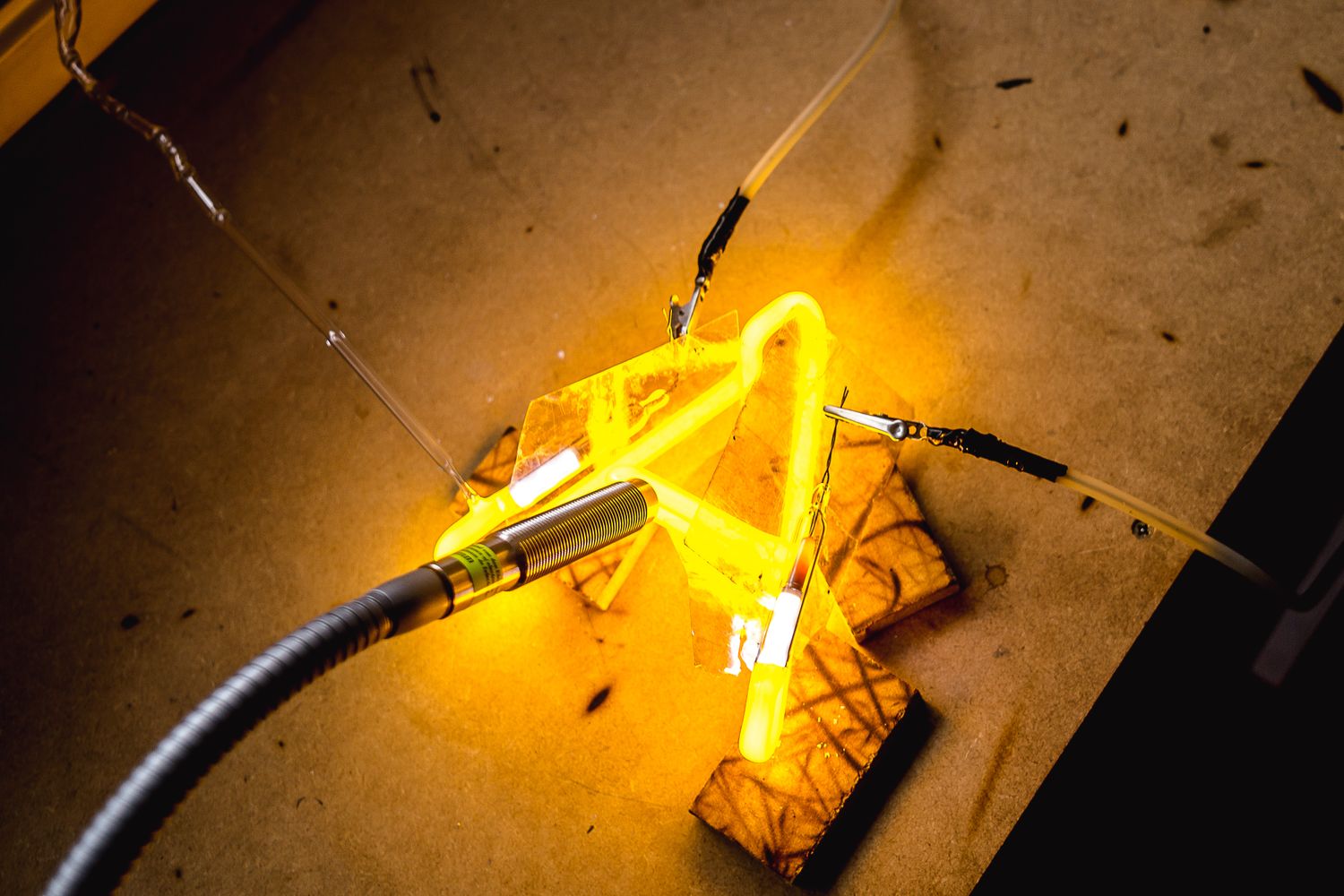
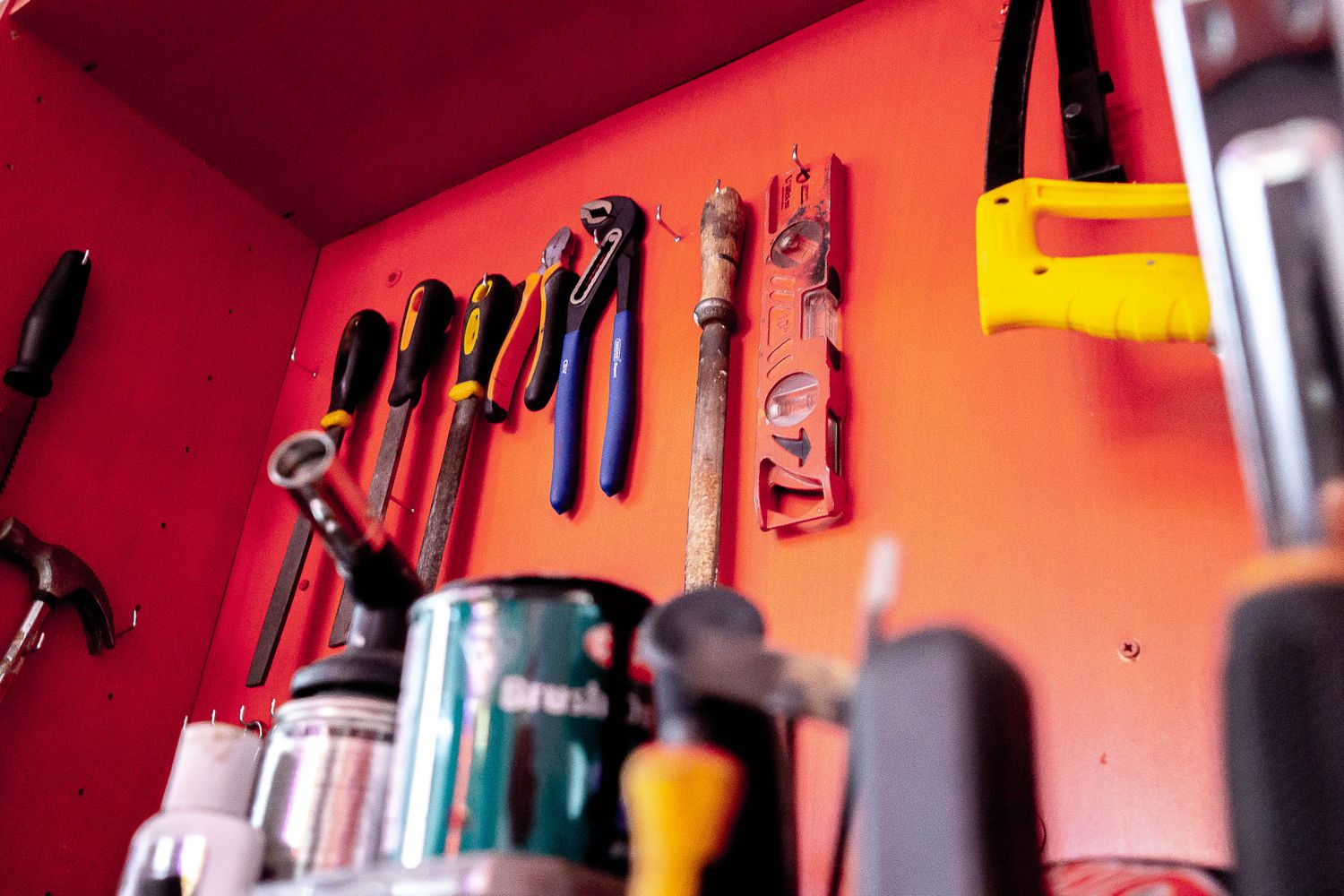
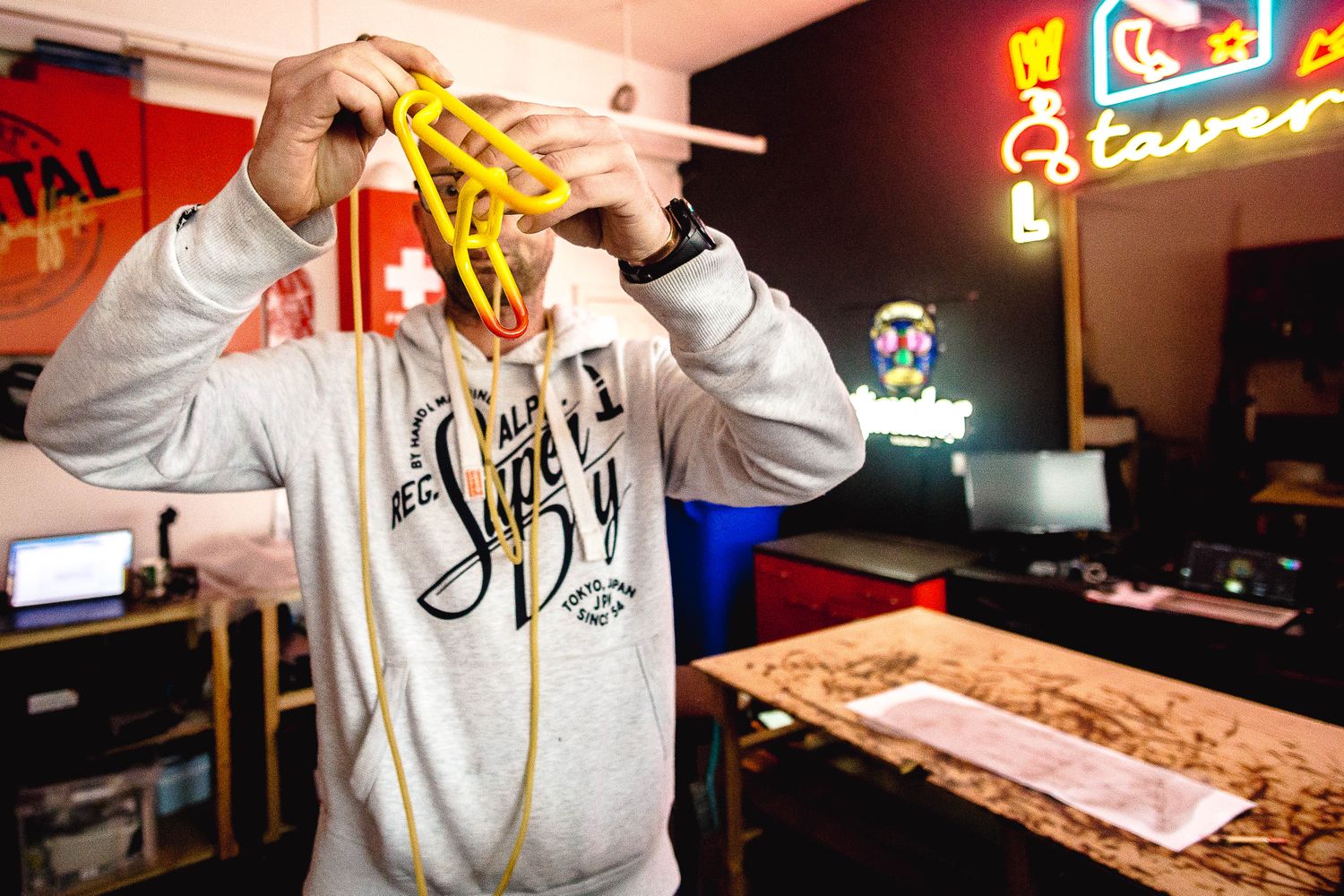
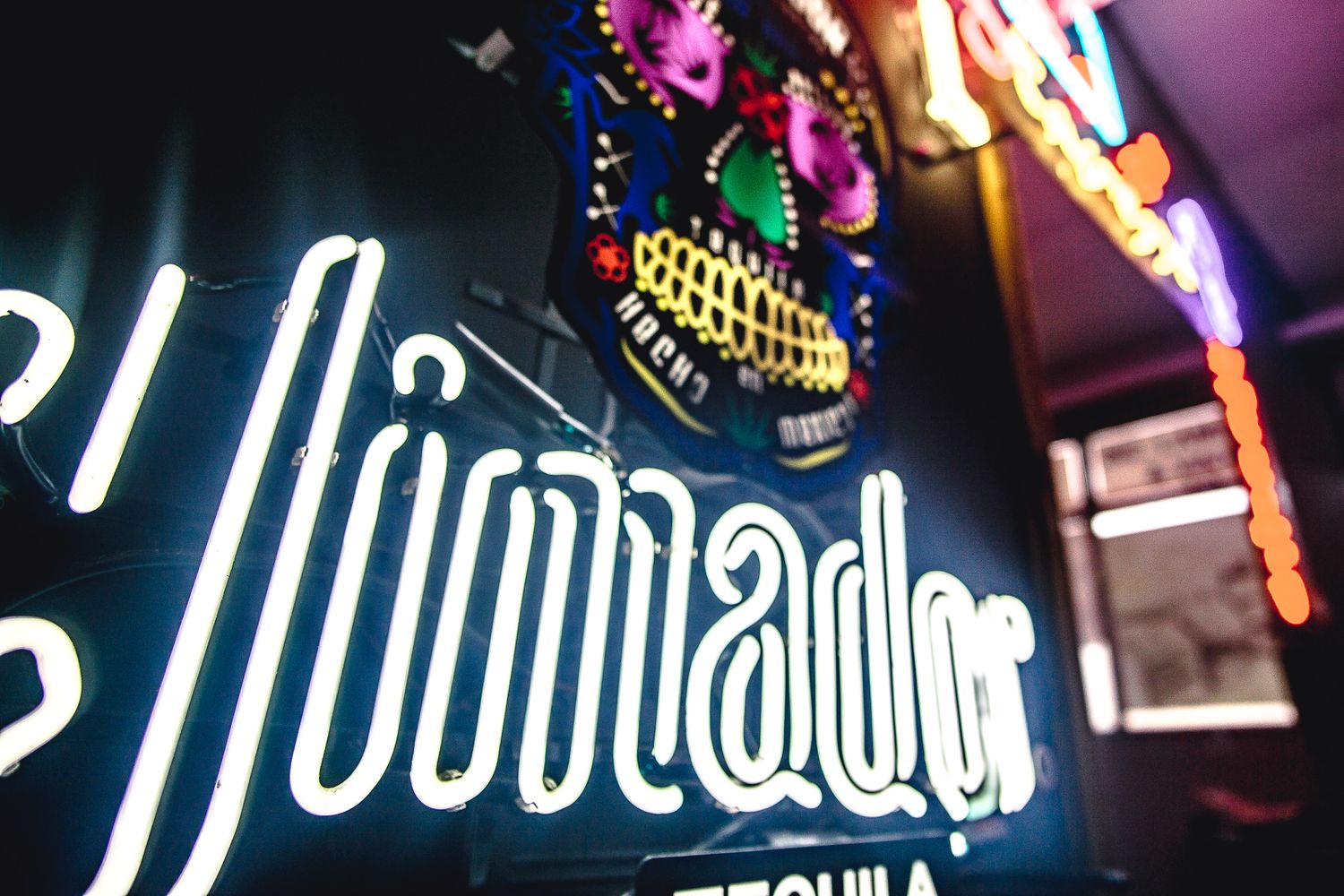
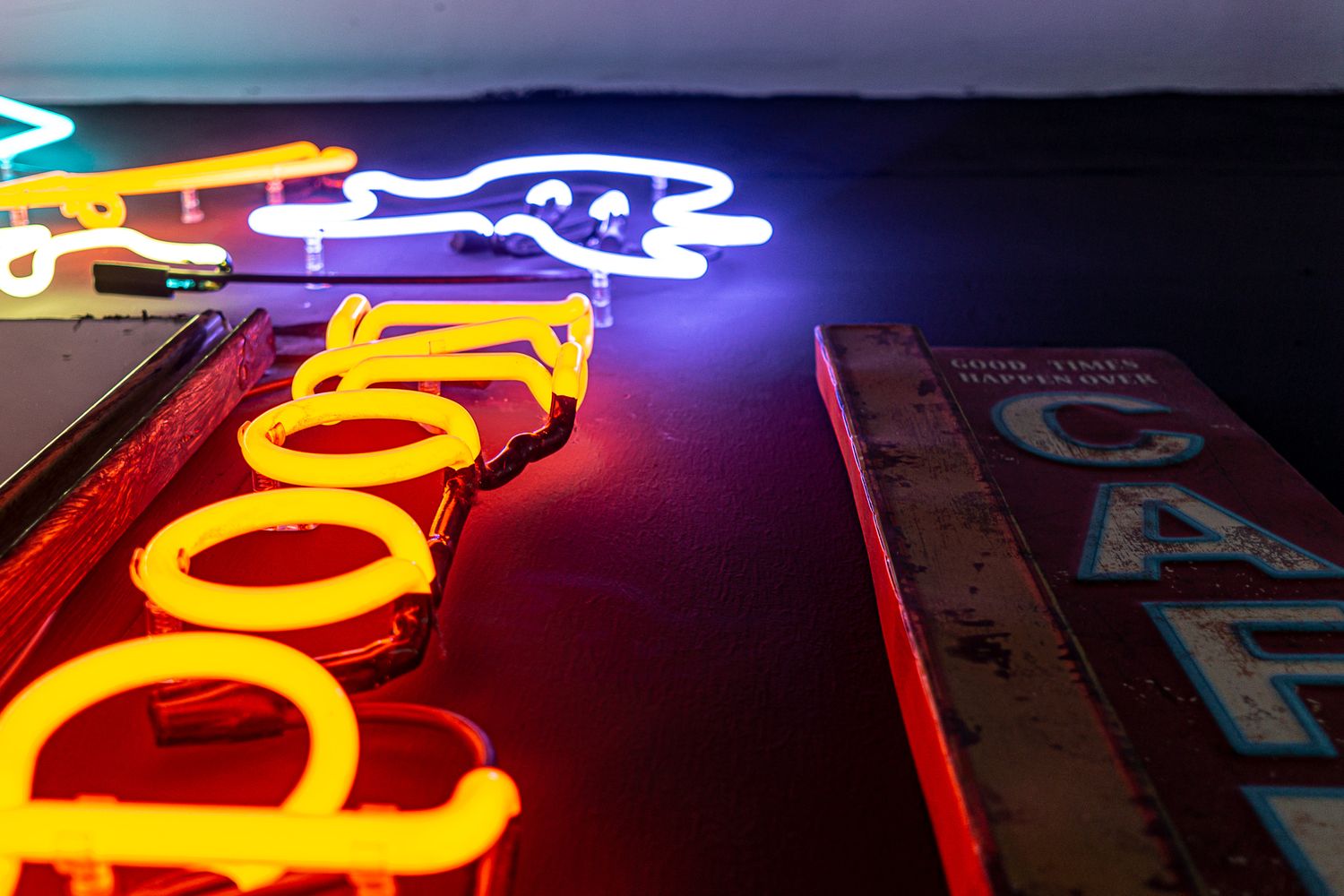
Tell us a bit about you…
I come from South Africa, Port Elizabeth. I studied graphic design but I grew up around neon signs, my bedroom was full of bits I’d recovered, recycled or revamped, and I collected them because my dad was a neon maker. So after I studied, I decided to help my dad. He began making neon in 1961 as an apprentice himself, and started teaching me properly in 2001 as a master glassblower.
Even with that background, I still can’t bend glass like him. Personally I think it takes a good ten to fifteen years of experience to get to grips with it and become a neon maker. I don’t think it’s a very easy thing to learn, and it does take a long time to be able to actually bend neon to a certain standard, but thankfully, the craft of making these signs is still alive.
Any strong memories of that time?
Yeah, we worked many hours together and there were always a lot of arguments, because he didn’t have a lot of patience. Now that he’s gone, I can admit I’m similar to that. I can see him standing there looking at me, and just saying ‘No, you’re doing it wrong.’ He wouldn’t tell me what I needed to do to fix it, he’d just make me start all over again!
In the beginning, I did all the joining of the electrodes and the gassing of the sections, while he would bend. We worked that way because that was our optimal speed, but in between he’d talk to me and teach me the little tricks he had up his sleeve – for example, a bend in the template might be too sharp to make in reality in the medium of glass, so he’d show me the off-the-cuff adjustments I could make to get around that. Nobody would notice it, but we’d know it was off-design. It was a lot of fun working with him.
One day he stopped fixing sections, got busy with other stuff – he loved vintage cars so he focused on that – and just left it all to me. Typically, without saying a word, that’s how he passed the mantle on and I became myself a neon maker.
What’s one thing people don’t know about you?
When I was eighteen I was in a horrible motorcycle accident. I was riding home from university and I was run over by a drunk driver. It impacted my life quite a bit – I can’t stand for long or walk really far – I take the dog around the block, but he is old and he’s got arthritis so it works out well. In fact we’re exactly the same! Jokes aside, I think the accident is a contributing factor to why I like doing neon, because I can still be creative, I still get to make stuff. It’s a physical demand I can fulfil.
Do you believe it takes a certain type of person to be a neon sign maker?
It’s not always possible to fix a bend in glass once it’s done, so you can’t rush. To be a neon sign maker you need to be a slower paced person, and remember to keep that pace, which can be especially hard living in the rat race that is London. I’ve had to remind myself more than once over the course of a decade.
There are a lot of parallels in how I am as an artist, with how I am as a person, a partner, a dog owner even – I’m not messy, I don’t drink, I’d rather hang out with friends at somebody’s house than go out to the pub and things like that. So I’m very chilled, a little introverted, and that all translates into my work somehow.
Does making neon still excite you?
Yeah, if I walk around Soho, I look at literally every single neon sign I pass. I don’t know what attracts me, it’s not just the colours and brightness, but the process that I know goes on behind it.
I just love making stuff – the connections with clients, the artwork, the sign, that exciting moment when you flip it on and everything goes off – or not! There’s always this sneaky little part inside of me where I kind of hope it doesn’t work, so I can find a fault, because there’s a lot of fun doing that – is it the wiring, is it something else?
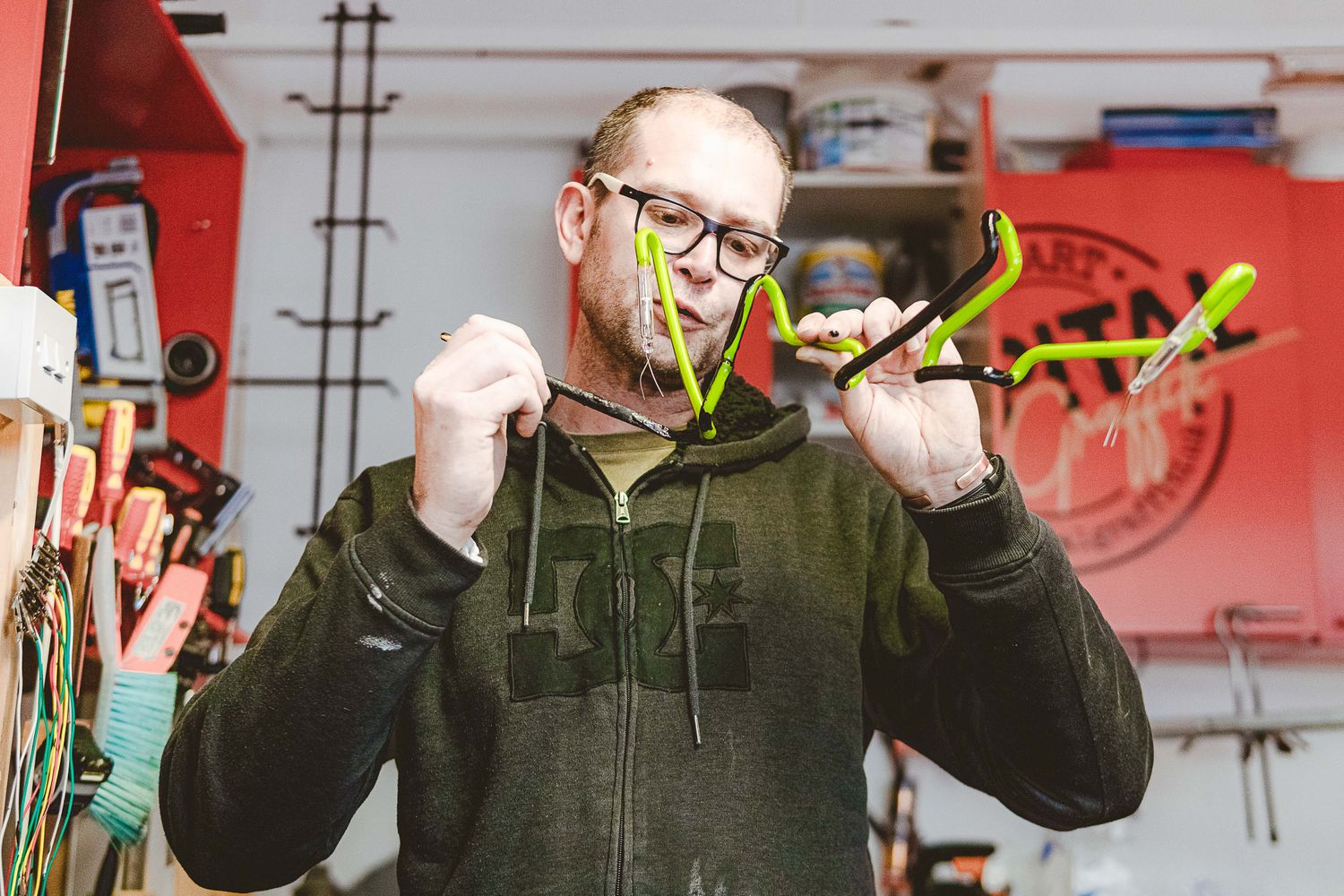
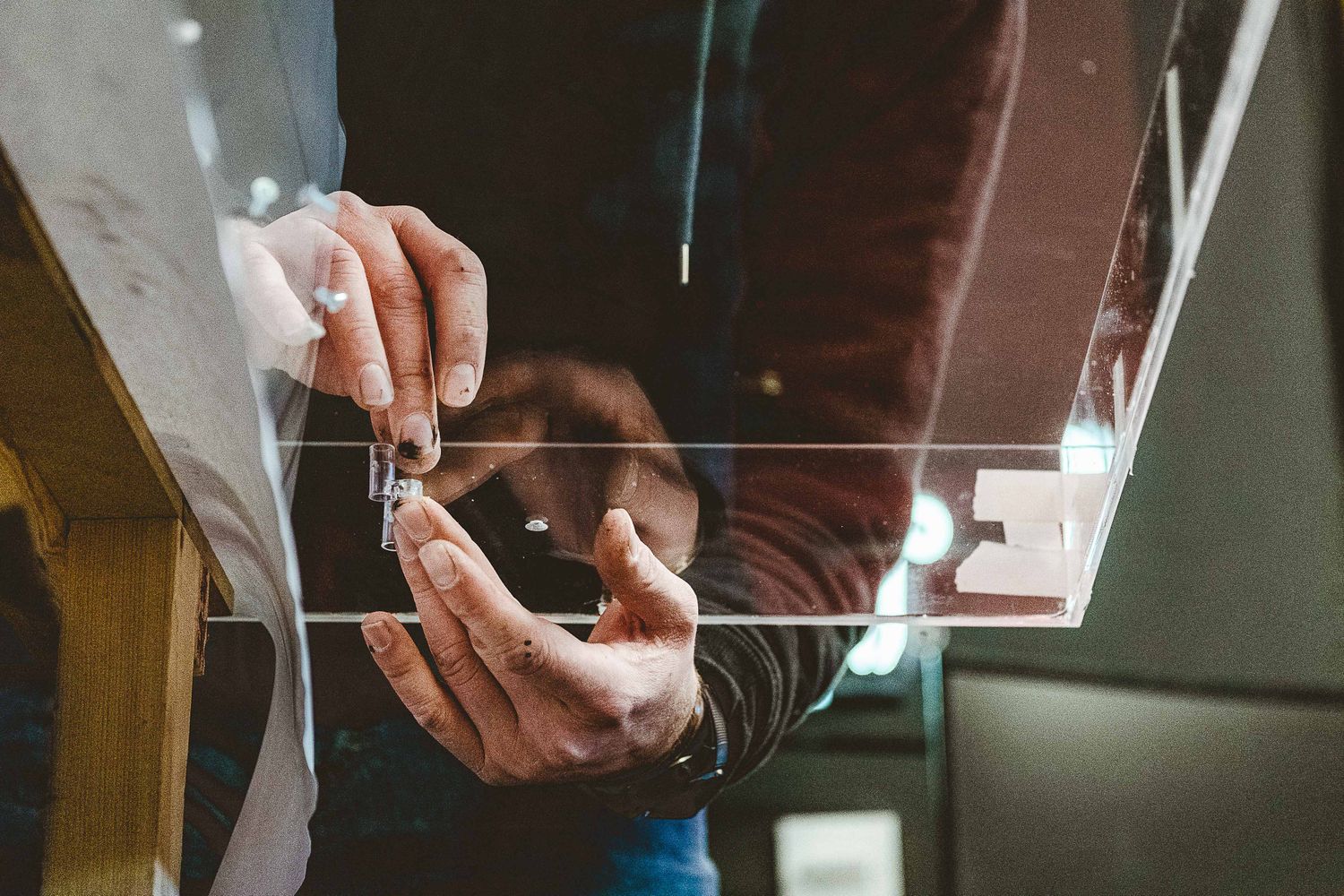
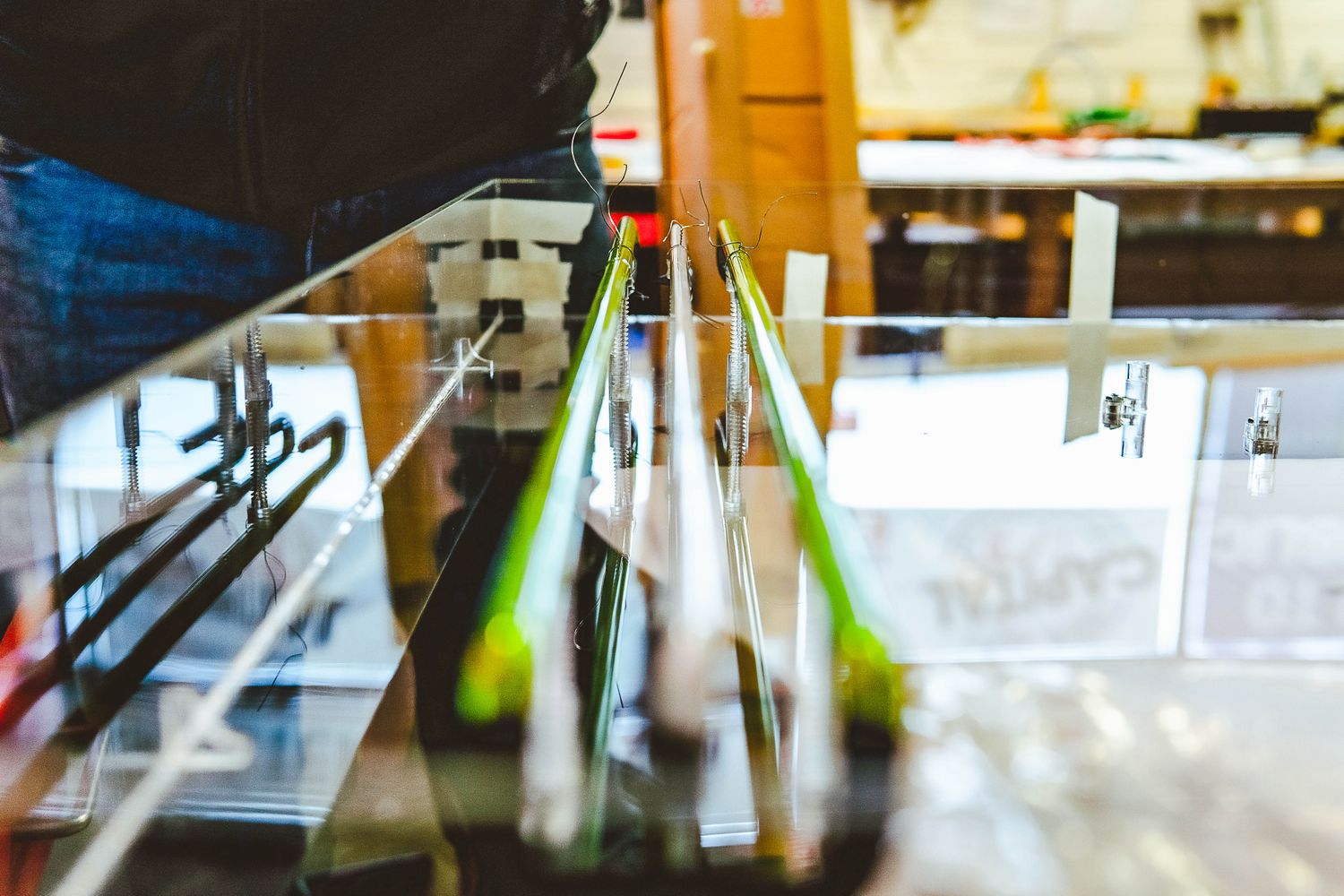
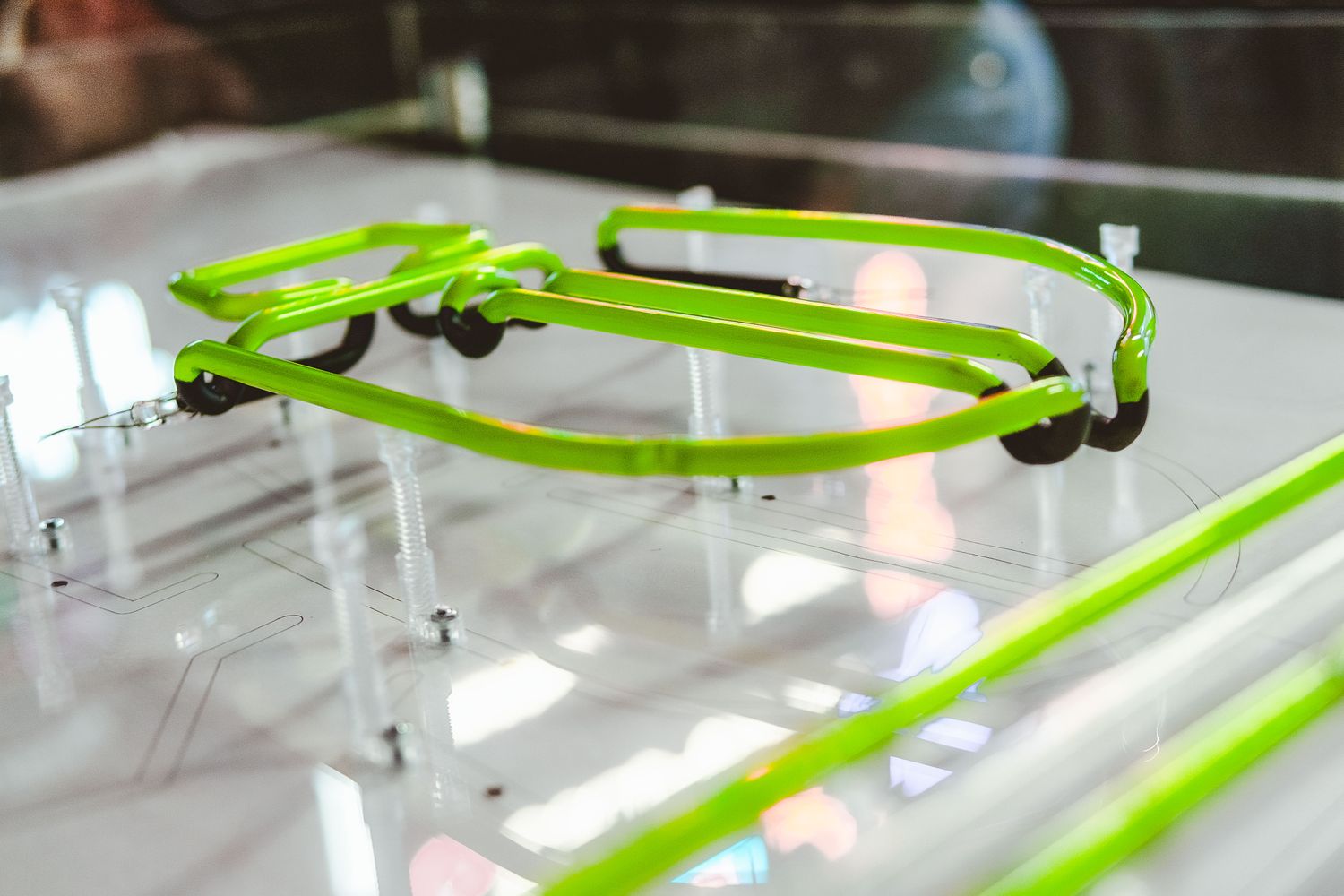
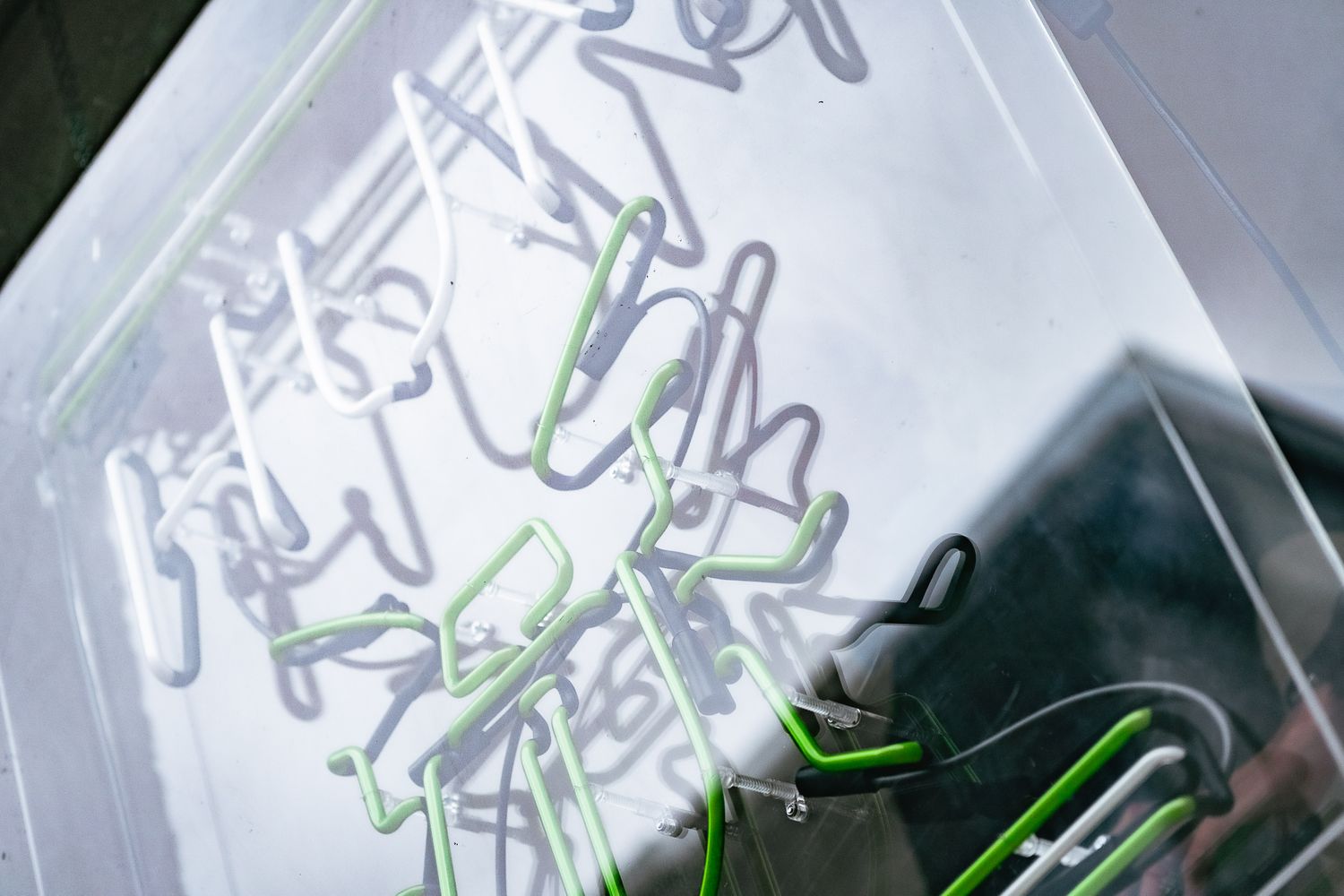
Are you still learning?
Yes definitely, always!
Why is neon so appealing?
It’s old. Everybody loves a sense of nostalgia. And it’s kind of upmarket these days. So if you have a neon sign – it attracts people, people want to hold on to everything with selfies and social media, and it plays on that. We do an incredible amount of photo walls.
The best is when you build neon straight onto a wall rather than pre-mounting it – piecing it together like a puzzle and fiddling with the wiring. All that anticipation, at the end the reaction is always just, ‘Wow!’
I’m proud when I have put a neon sign up, and I think the customer who owns it feels proud as well. Every time I install one, it’s the only one in the room, and it doesn’t shine like regular lighting – it glows. It gives off this soft aura that changes the ambience, and people’s mood.
I love that when I’m creating neon, I’m also creating this hypnotising atmosphere for people to experience, further down the line.
Are you creative in other ways?
I studied fine art for four years before specialising in graphic design, so yeah I do paintings and sculptures, but I more enjoy physically building a finished, functional product. I just love that neon starts from a flat sheet and when you’re done it’s this pulsing sign that blows your mind when you switch it on.
Who inspires you?
Tracy Emin, of course, her neon handwriting is amazing.
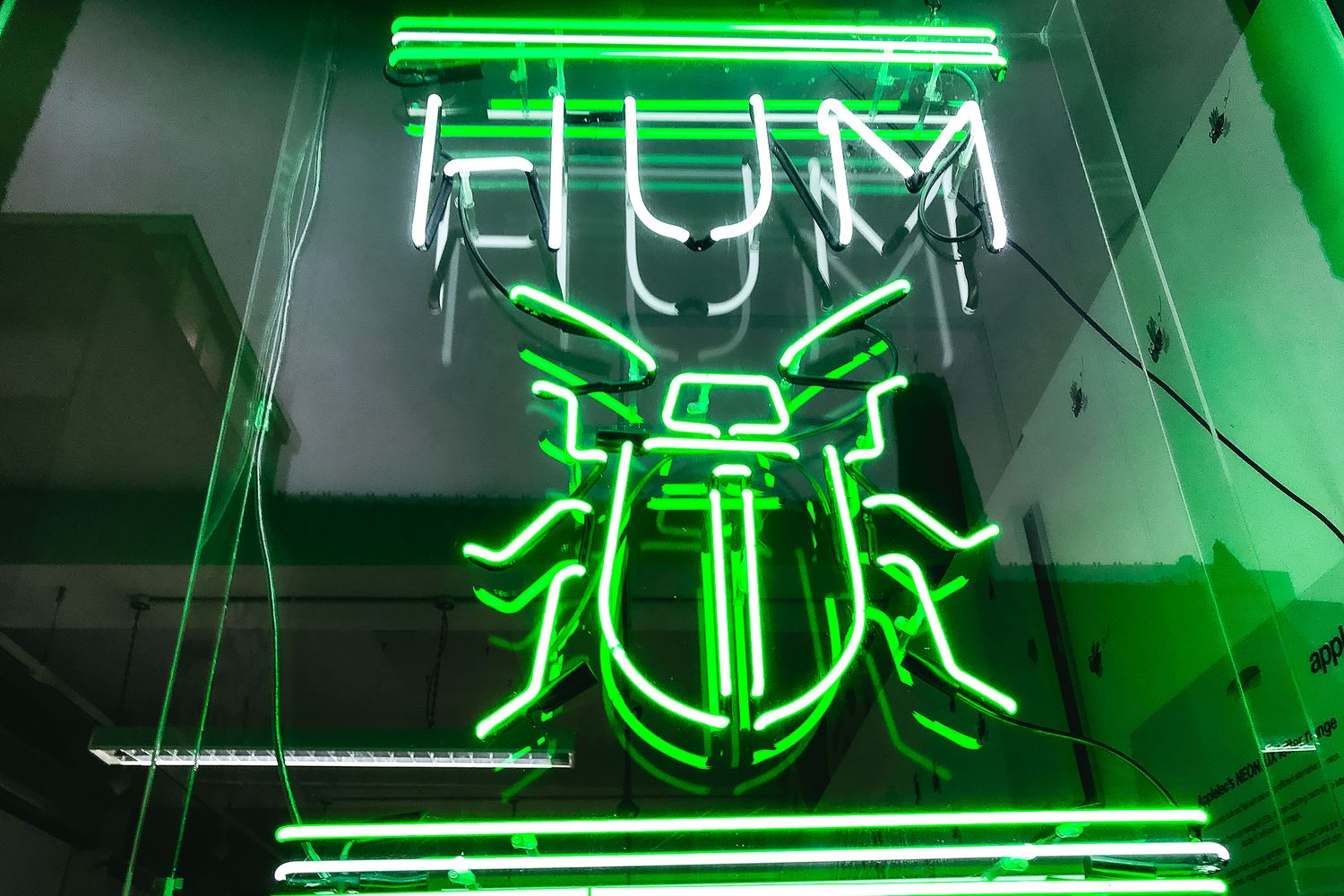
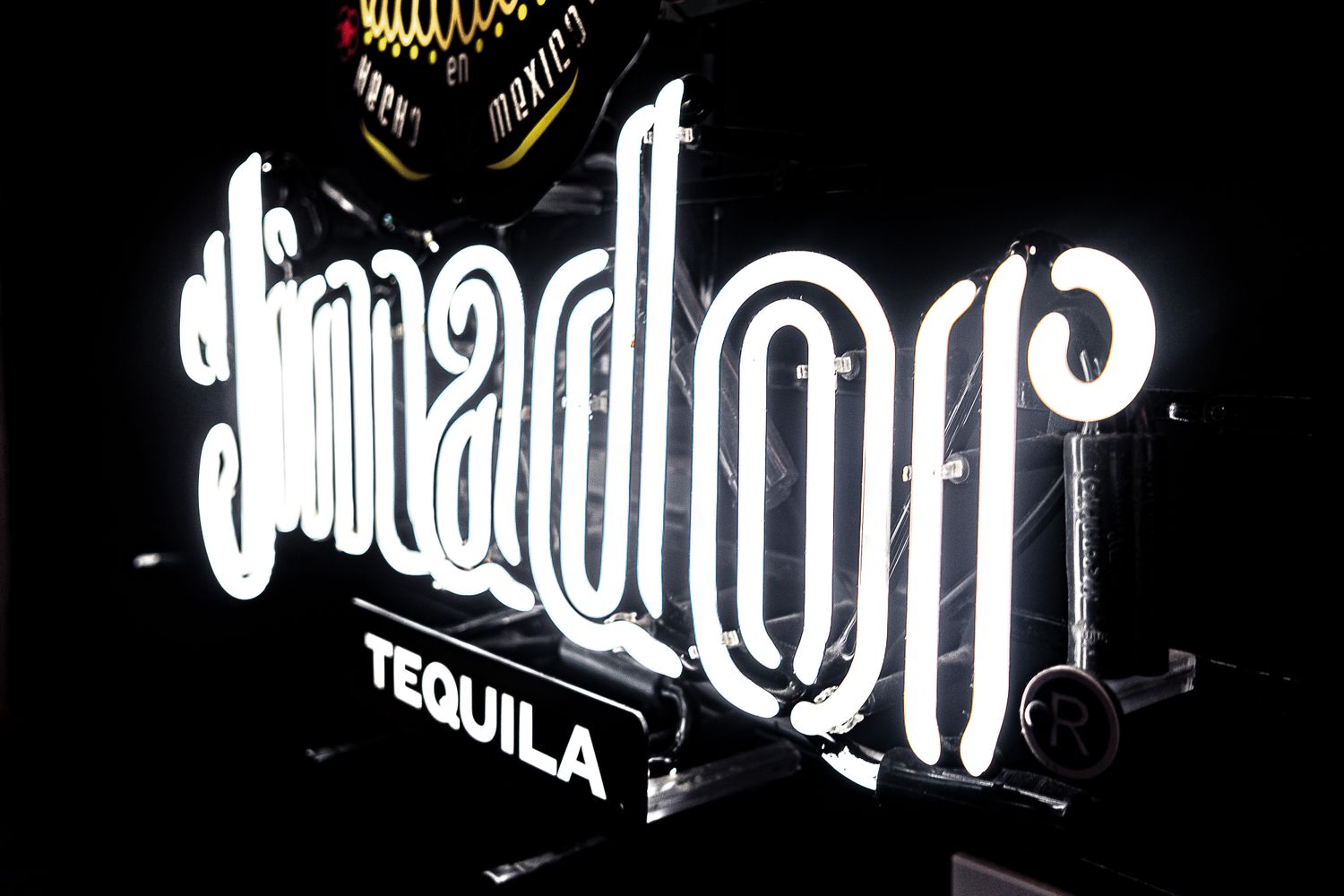
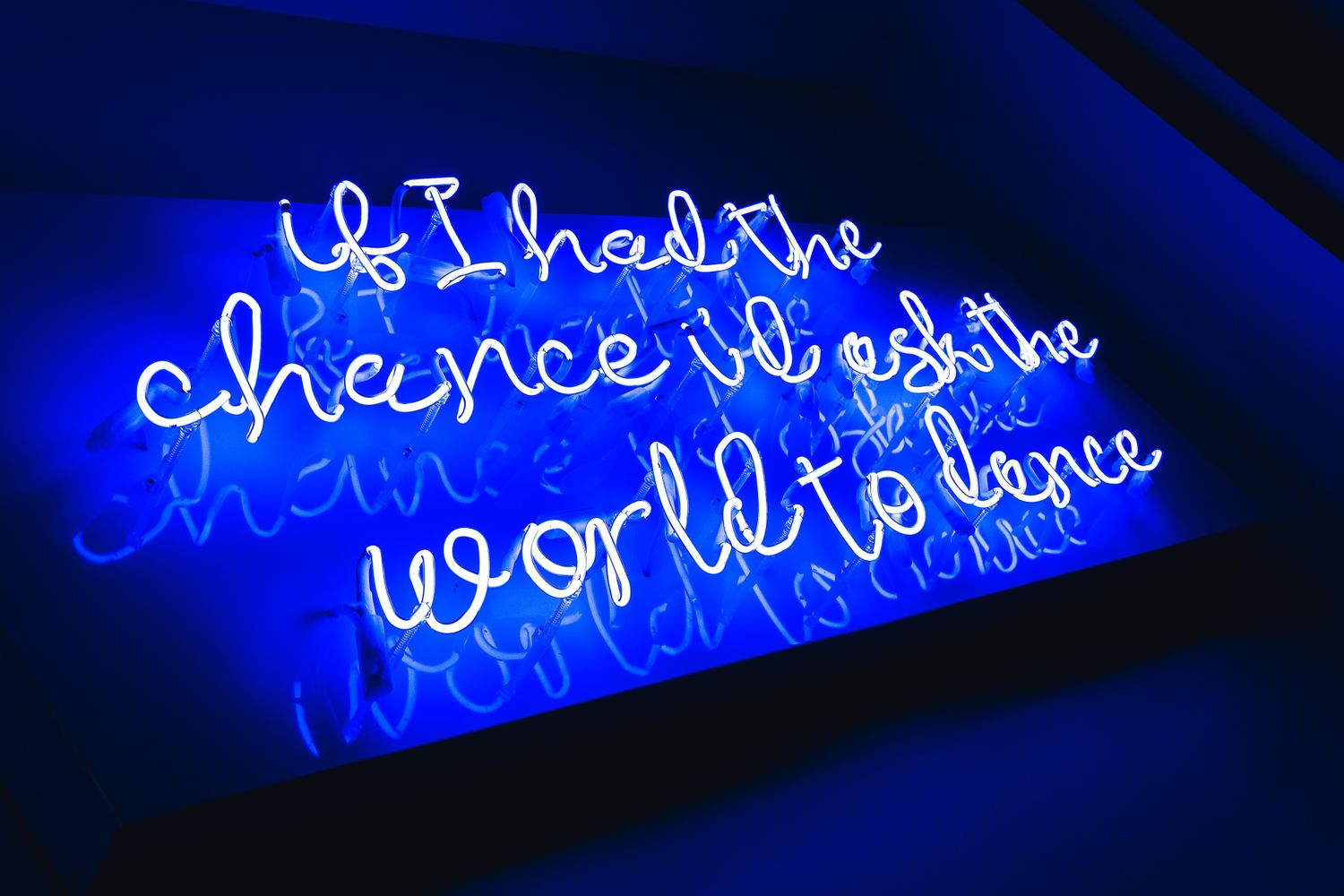
Do people underestimate the work that goes into that?
It is much more difficult to make neon in script fonts than block types, because you literally have to heat up every millimetre of the glass to make those flowing, handwritten shapes.
Can you walk us through the creative process?
First we print a full size rendering of the artwork in reverse and set the paper down as a template. My personal preference is to have aluminium mesh to put over the template as a protective barrier, because the glass gets so hot it will actually set the paper alight.
With the template to help, we mark on the glass where we want to make our first bend, and heat that up using a ribbon burner or crossfire torch. When glass tubing becomes molten, it collapses flat, so we use a pipe to blow into it, keeping the diameter open while making the bend.
Rinse and repeat till the tube takes the shape of your template. We finish the sign by extracting impurities with a vacuum system and lighting the tube up using these little silver electrodes, which, when electrified, ignite the gas inside.
The last step is then to mount a power transformer to the piece. It doesn’t matter how long you’ve been doing this, every single time you flick the switch on a sign for the first time, it’s really exciting.
If you follow the process properly, you’ll have a sign that lasts you at least 10 years.
Where does the luminous quality of neon come from?
In the commercial craft, there are mainly two gasses used – one is Argon, which with a drop of mercury, imparts cooler, bluer hues, and then you get Neon gas, which is my favourite, a warmer, bright red. There’s also Xenon and a few other gasses but they’re not as vivid, and not as widely used in the industry.
The hue and brightness of the sign depends on the type of gas, and the tint of the tubing. Combining those two things you can create a lot of different colours: Warm Tone White or Flamingo Pink for instance, Orchard Purple, Super Blue, Powder Blue Midnight Blue, a type of turquoise called Seacrest, Lime Green, Emerald Green, Novell Yellow, Ruby Red, Citrus Orange…the possibilities are endless.
Do you think making it is an art form?
It takes a long time to learn to be a neon sign maker, a lot of experience, a lot of practising, patience and precision. The fact is that there’s a very small amount of people that can actually do it, that can understand how the glass will react. So yes, it is an art form, you’re creating something great, and it’s handmade.
What are some of the challenges of being a neon sign maker?
It’s about working with a continuous piece of glass, bending without making a joint, because if there’s a break anywhere, the piece won’t light up as a whole. So if you imagine unravelling a neon sign, you’d get a long, straight piece of glass. That’s one thing, and of course, it can get very hot. In South Africa, some days it touches almost 50°C. Even in London, last year I think one day it got to 38°C outside, and it was 49°C here in the studio.
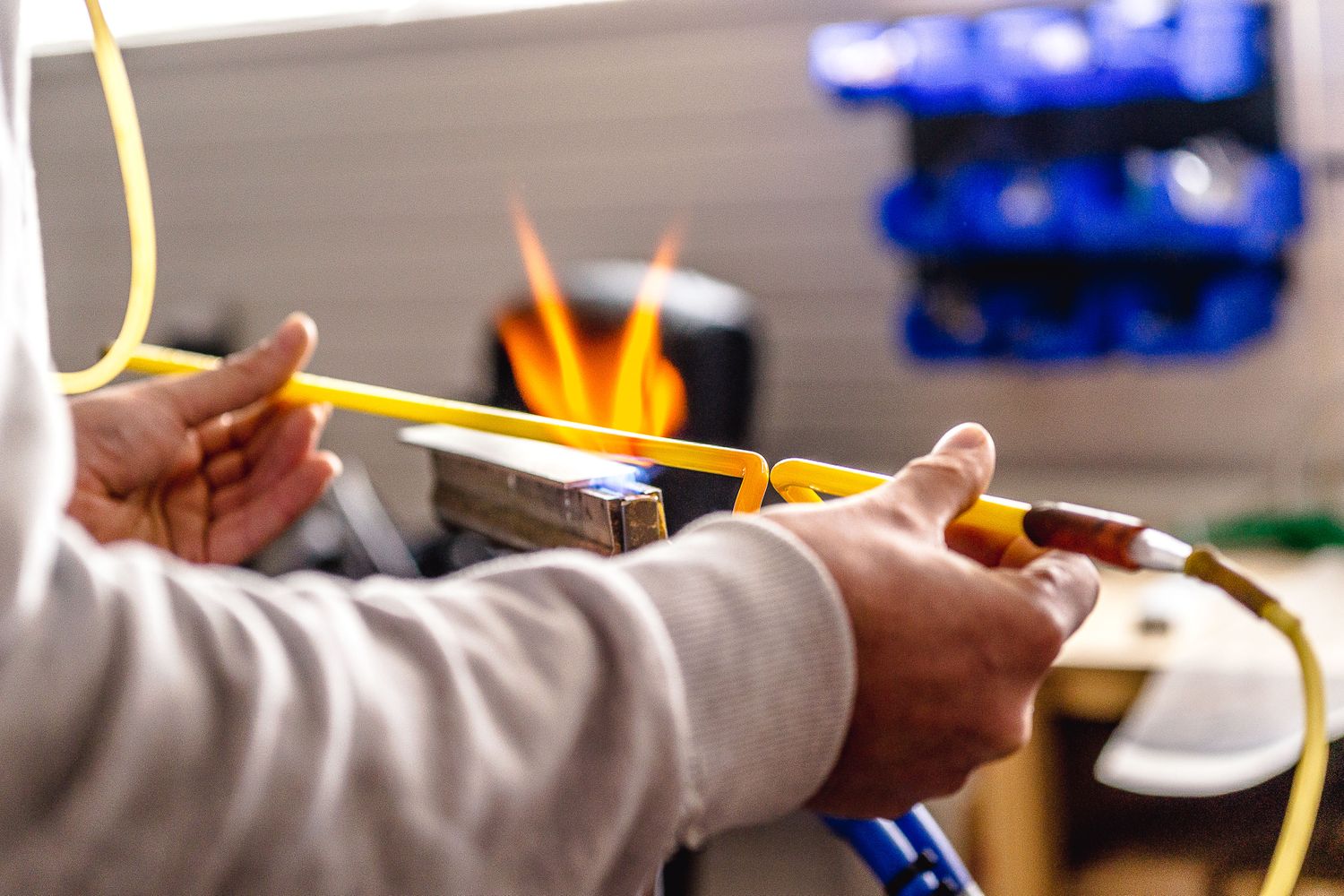
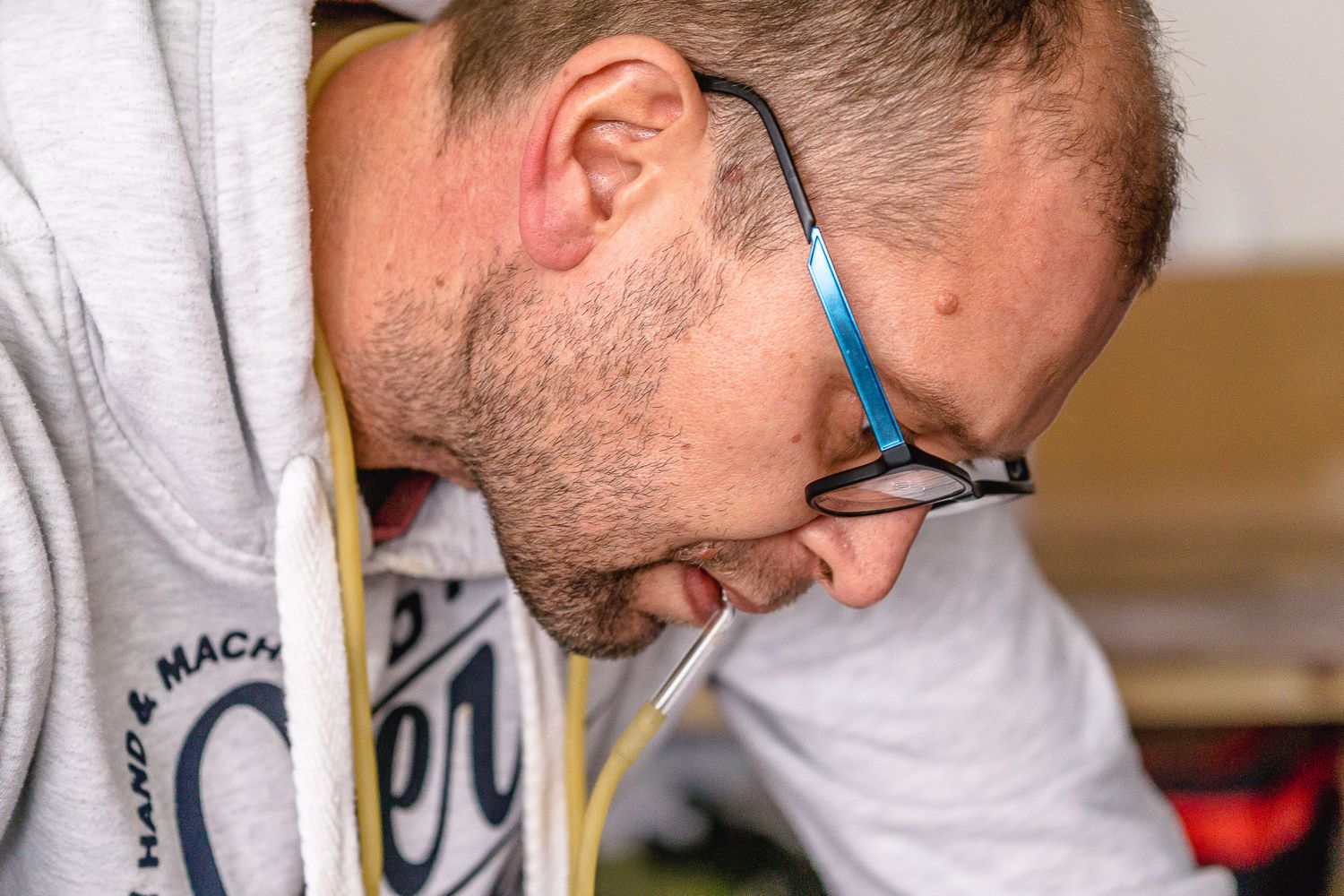
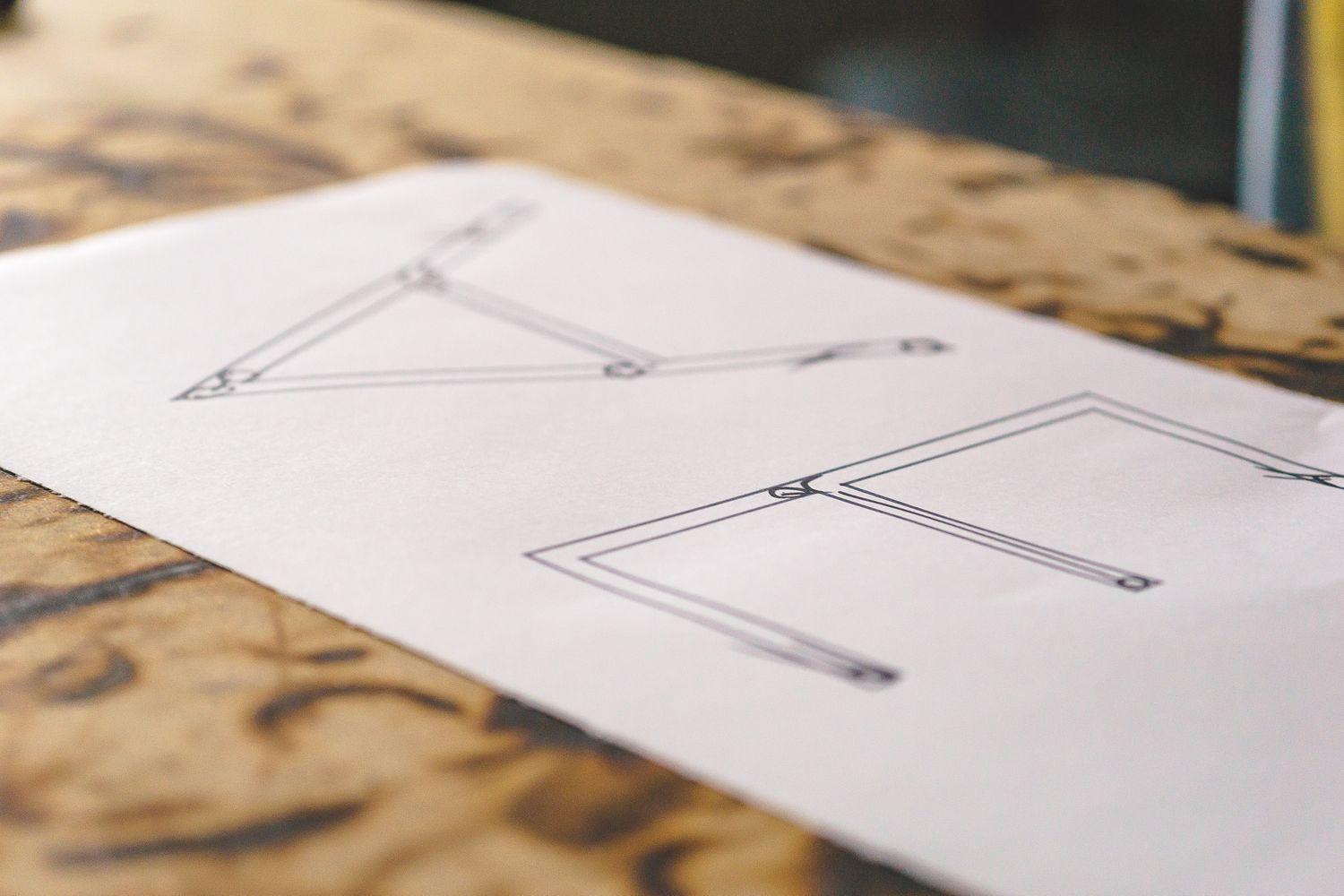
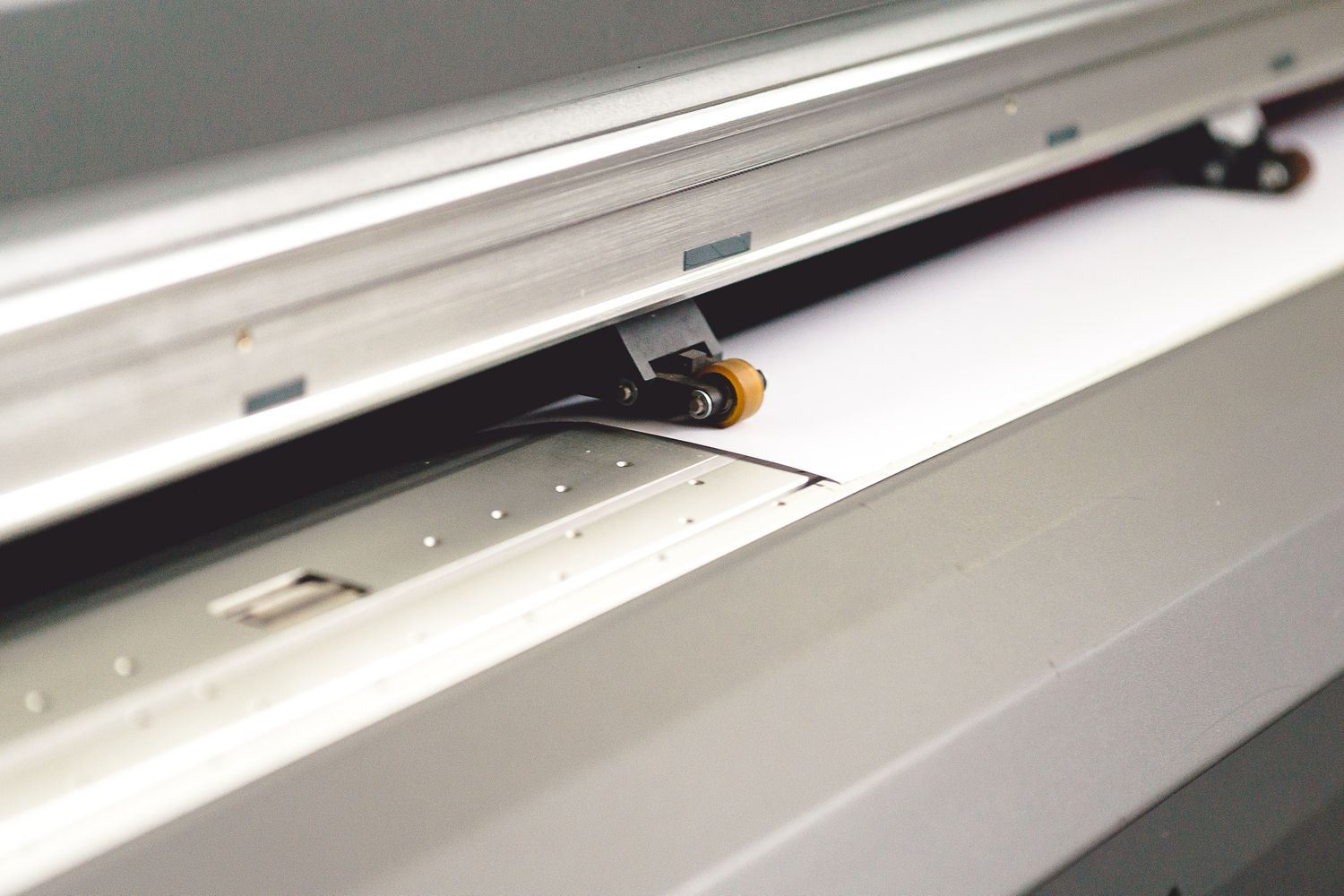
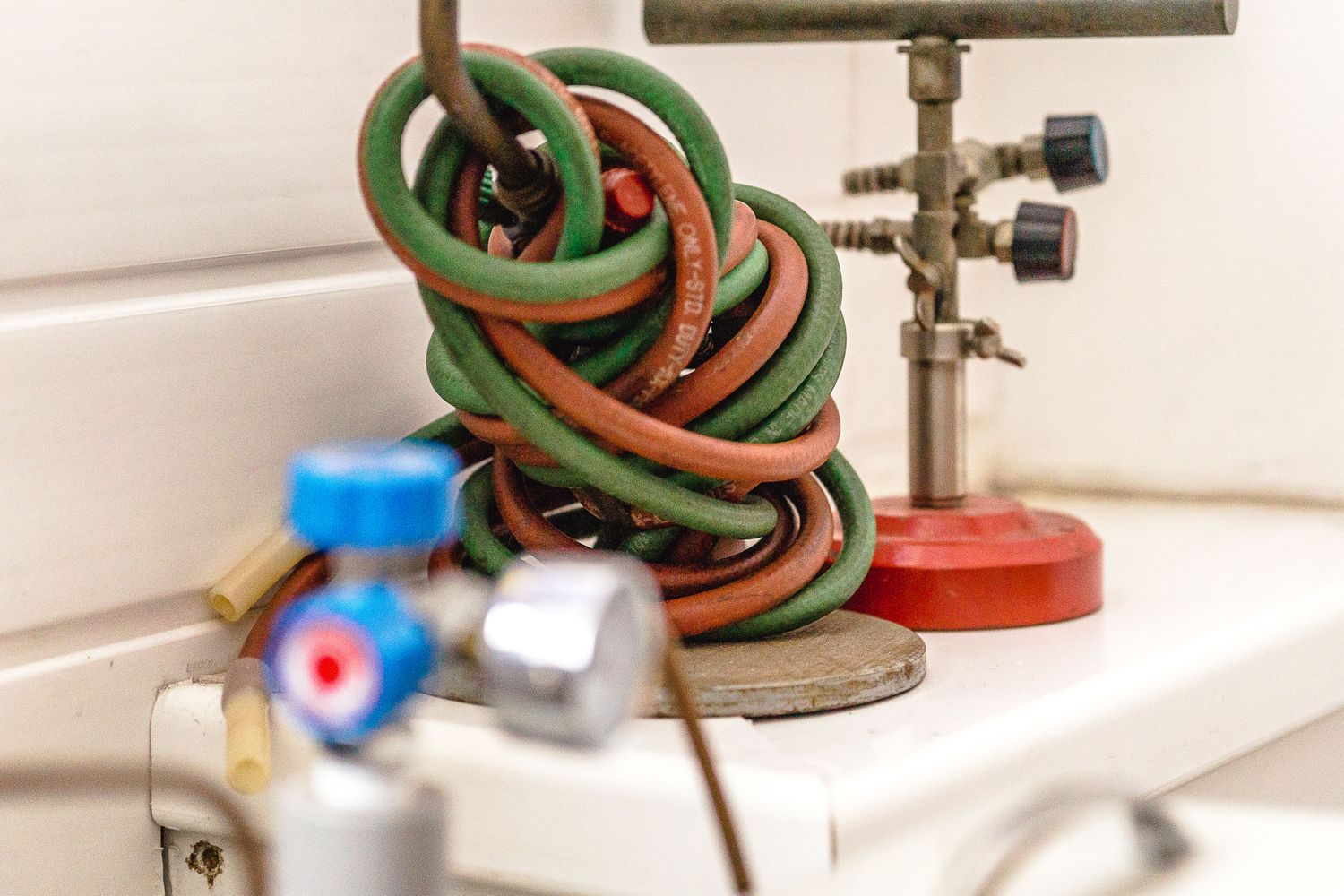
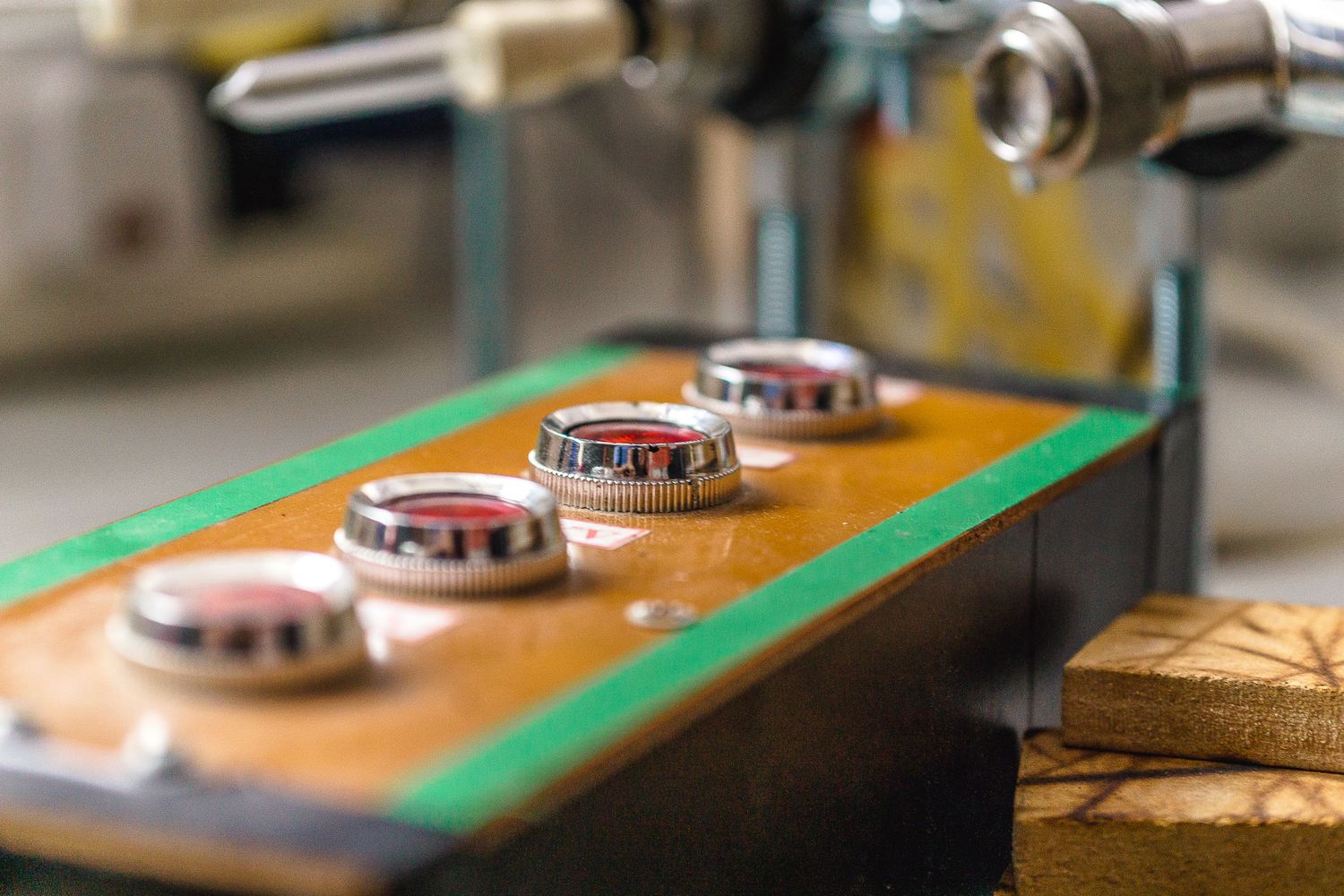
How do you zone out / focus in?
While I love my 80s’ music, I’ll tune in to whatever’s on the radio – as long as I can hear voices, I’m happy, I like that sense of having people around me – but yeah, I don’t zone out. Neon is high voltage and there is a certain risk to it sometimes.
There’s a lot of concentration involved because you need to remember exactly where you heat up, because if you don’t and you touch that spot, you’re going to burn, and it’s very painful – blisters and everything.
That’s another challenge – it’s actually quite hard to find people who want to learn the process, because as soon as people hurt themselves, they kind of lose interest or get afraid of it. Of course, that’s natural, there’s some days when I’ve burned myself because my concentration is not where it’s supposed to be, and I’m more wary.
What’s been your worst injury?
It was probably the beginning of the year where I kind of burnt off the fingerprint on my thumb, it was completely gone and the skin was stuck to the glass – it freaked me out, that freaked me out actually more than the pain and everything else. I couldn’t open my phone. I had to put in the code every time, because it just was gone! It took a while to heal, but I’ve got my fingerprint back now.
A sign you’ve found hard to give away…
My favourite project was for a gentlemen in Chelsea and it was an infinity sign. So basically what that is, is a mirror, then some neon, and a mirror. Together, it makes it look like you have infinite layers of neon instead of just one, creating this loop that you can just get lost in.
They’re generally not difficult to do, but the bigger they are, the better in terms of impact and challenge – this sign had the word ‘discretion’, getting seemingly smaller as it went backwards, and it was four metres by two and a half metres in size. Imagine making panels with mirrors that big! I enjoyed that and must admit I got a bit sentimental about giving it away.
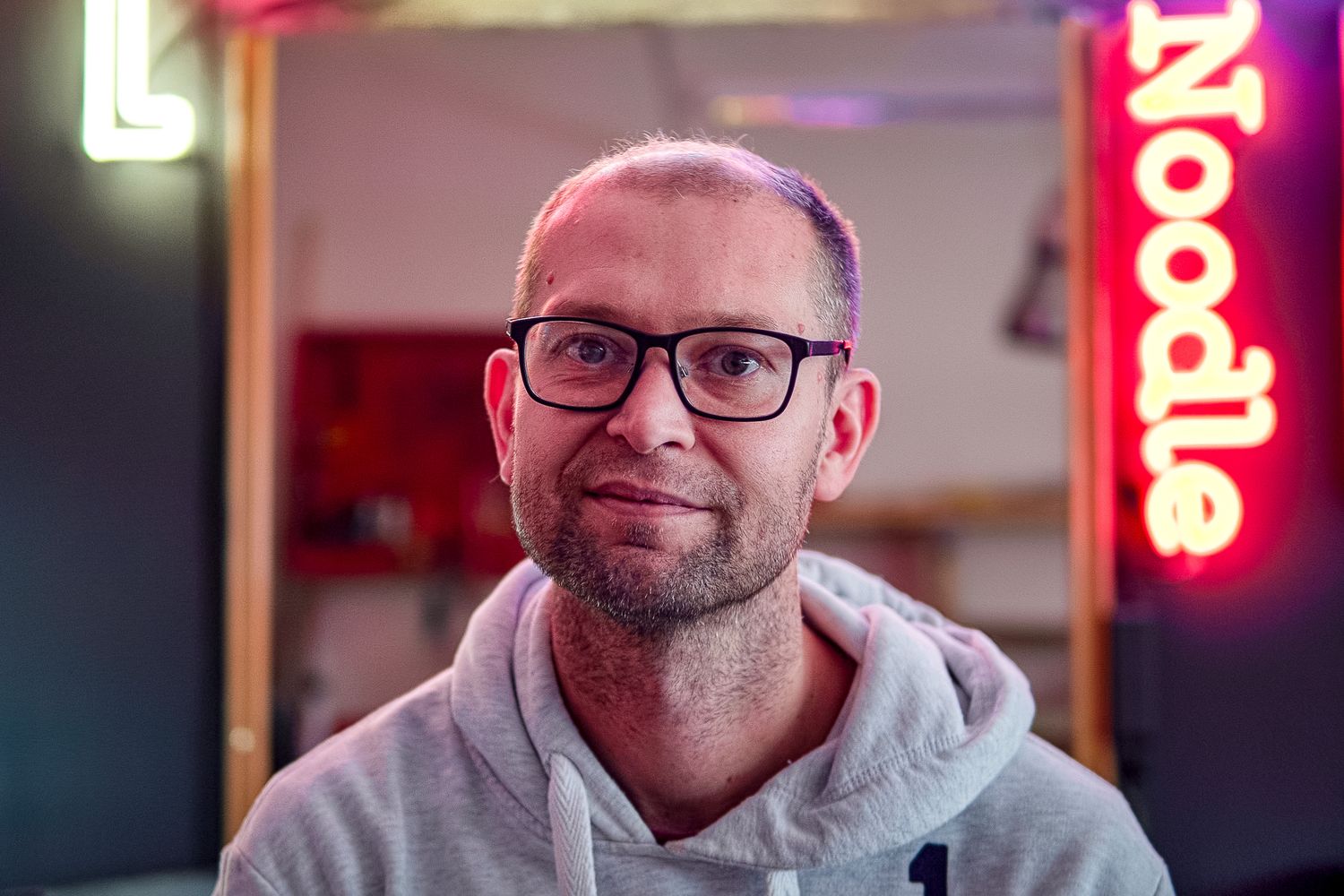
Is there an all-time iconic piece for you?
I had this blue moon with a yellow saxophone in my room from childhood, and whenever I see something jazzy like that it makes me think of South Africa. It’s a connection all of my own.
Generally speaking, neon is much bigger there, it’s a very common visual medium. You have your regular alcohol signs – even the petrol garages have it as standard, with outlines around the canopies and stuff. You just don’t see that casual use here.
So is it harder to survive as a neon artist here?
Yes, there’s not many glassblowers in the UK left – in London there’s only basically two. LEDs are taking over, and making real, traditional neon is a tedious and long process, but saying that, what goes around comes around. People appreciate the handmade, technical nature of true neon.
I personally prefer it here – I get to work on creative commissions and on personal projects for people’s homes. It’s not your run of the mill stuff, it’s all pretty cool. I’ve a lot of freedom of what I design and do – my briefs are often just a slogan, and then the artwork to depict that is up to me, so at the end of the day it’s almost 100% my creativity.